What if you could hold onto your used equipment
until you need it again?
With companies navigating new virtual environments, staffing shifts, and changing IT hardware needs, flexibility has become more valuable. With that in mind, Summit 360 is leading the way in offering new redeployment solutions to meet our clients’ changing needs. As equipment comes back from staff or locations, we’re able to shelf, kit, and configure it for its next stage of life. As a result, we’re helping businesses eliminate the cost of investing in new equipment while extending the life of their existing hardware and impacting the planet.
Hardware redeployment solutions that
meet your changing needs.
Convenient Storage Options

One of the reasons many businesses lean toward eliminating used equipment is the need to store it when it’s not in use. Even though they may need it again in a matter of months, the space required to store it and the resources required to manage that storage can represent a barrier.
At Summit 360, we’ve removed this barrier by providing the storage solutions you need to shelve your hardware until you need it again. We’ll even coordinate the logistics and transportation so you can focus on other parts of your business.
Efficient Inventory Controls & Tracking

When it comes to inventory control, many small and midsize companies (and in some cases the largest companies) are still using simple spreadsheets to track their assets and hardware. It’s simply not a core competency or focus of the business. From a redeployment perspective, this makes accurate equipment tracking almost impossible. Then, even if they know they have a piece of needed hardware, they need to recall where they stored it. This “process” is inefficient and unorganized.
At Summit 360, our inventory control solutions allow our clients to easily see what they have and where it’s located, making redeployment quick and straightforward.
Testing, Repair, and Configuration
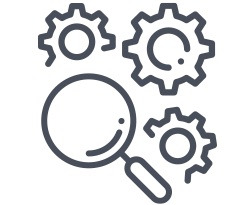
Before hardware is deployed back into the field, it’s vital that it is meticulously tested for defects and failures.
At Summit 360, our redeployment process includes rigorous inspection, making essential repairs as they’re needed, configuring hardware, and imaging software so that it is ready for use upon arrival. We evaluate every piece of equipment we redeploy to ensure it performs like new for our clients when they need it most.
Custom Kitting Based on Your Needs

During our redeployment process, we’re not only testing, repairing, imaging, and configuring client hardware, but we’re also kitting it. This involves ensuring that each piece of hardware is accompanied by the accessories it requires to operate – the same as it would show up in a new, unopened box, or even better with custom kitting based on your company needs.
From data cables to power to keyboards, our redeployment process includes sending equipment back out to our clients with everything it needs to work – right away.
Security-Focused Redeployment
